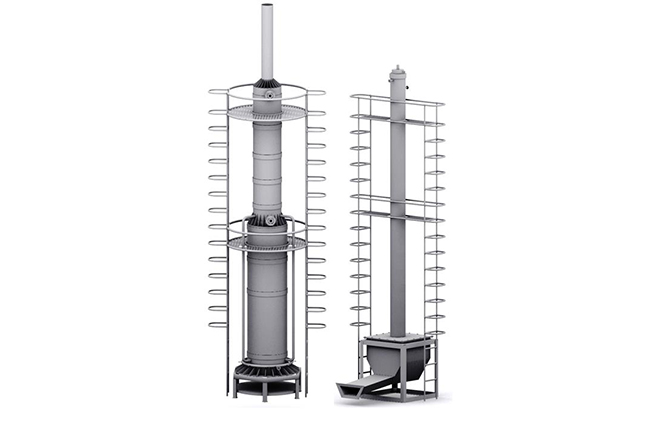
Комплект оборудования для реализации процесса непрерывного коксования
Базовый комплект оборудования включает в себя реактор крекинга и шнековый реактор, дополненные оборудованием обвязки (теплообменники, сепараторы, конденсаторы, насосно-компрессорное оборудование, активатор или дозирующее оборудование). Дополнительное оборудование может быть поставлено опционально, либо в качестве него использовано существующее оборудование эсплуатанта базового оборудования. Оборудование позволяет осуществлять переработку мазута в легкие и средние дистилляты с суммарным их выходом порядка 76-82% от массы прямогонного мазута марки М100. При переработке мазута не образуется остаточных темных продуктов.
Технологическая схема реализации процесса
Исходный мазут, с температурой обеспечивающей его текучесть, подается насосом Н1 в проточный гидродинамический смеситель ГС1, где смешивается с раствором катализатора на основе ультрадисперсных частиц железа, дозируемый насосом дозатором НД1 из емкости Е1. Рабочая концентрация катализатора 10мкг/кг. Цель ввода катализатора – дестабилизация устойчивой коллоидно-мицелярной структуры мазута, образованной асфальтено-смолистыми соединениями, что необходимо для предотвращения адгезии кокса к поверхности оборудования на дальнейших этапах переработки мазута.
ИЛИ
Исходный мазут, с температурой обеспечивающей его текучесть, подается насосом Н2 в электромагнитный активатор А1, где происходит дестабилизация устойчивой коллоидно-мицелярной структуры мазута, образованной асфальтено-смолистыми соединениями. Цель активации – предотвратить явление адгезии кокса к поверхности оборудования на дальнейших этапах переработки мазута.
Активированный мазут предварительно подогревается в теплообменном аппарате ТО1 и ТО2 за счет тепла углеводородной парогазовой смеси (УПГС) – продукта крекинга и коксования соответственно. Предварительно подогретый мазут поступает в печь-реактор ПР1 окислительного крекинга, где при температуре 450оС происходит его разложение с образованием тяжелого крекинг остатка (ТКО) и УПГС, содержащей пары светлых углеводородов. Процесс крекинга активируется подачей воздуха (1,5л/кг). Подача воздуха производится посредством газодувки Г1. ТКО подается на шнековый реактор крекинг-коксования ШР1, где происходит его окончательное разложение с образованием дополнительного количества легких и средних фракций и кокса. Выгрузка кокса из бункера шнекового реактора происходит в непрерывном режиме. Захолаживание («тушение») кокса происходит путем подачи в бункер водяного пара.
УПГС с процессов крекинга и крекинг-коксования после частичного охлаждения в теплообменных аппаратах ТО1 и ТО2 за счет передачи тепла мазуту, поступает в холодильники-конденсаторы ХК1 и ХК2. В холодильниках-конденсаторах происходит конденсация жидких углеводородов, которые отделяются от горючих газов в сепараторе С1, а далее от водяного конденсата, который используется для выработки пара, в сепараторе С2. Жидкая фракция после сепаратора является целевым продуктом – широкой фракцией углеводородов (ШФУ) с КК350-360оС. Горючий газ используется для собственных нужд в качестве энергоносителя (газ предварительно сжимается газодувкой Г2 и сжигается в горелочных устройствах, избыточные количества газа сжигаются на свече или используются для выработки электроэнергии посредством газопоршневой установки). ХК1-ХК2 могут быть заменены на ректификационную колонну.
Базовое оборудование
Базовым оборудованием являются печь-реактор для проведения процесса окислительного крекинга и шнековый реактор для реализации процесса коксования. Оборудование имеет высоту 6-8 метров высоты (не считая дымовых труб) и диаметр основания от 1100 до 1600мм в зависимости от производительности (1500- 3500кг/час). Оборудование может быть размещено на расстоянии не менее 15 метров друг от друга и другого оборудования с организацией аварийной паровой завесы.
Печь-реактор спроектирована по принципу жаротрубного котла. Подаваемый воздух для инициирования окислительного крекинга, также необходим для турбулизации потока и исключения застойных зон. Шнековый реактор сконструирован по принципу роторного устройства, шнек одновременно используется для выгрузки кокса в бункер, откуда последний выгружается через шлюзовое устройство с поровой защитой от подсоса воздуха в реактор.
Вспомогательное оборудование
Дополнительное оборудование может быть поставлено опционально, либо в качестве него использовано существующее оборудование эсплуатанта.
Пример переработки для оценки окупаемости
Сырье:
- Мазут марки М100 (прямогонный, содержание серы 1,7%) – 100%
Продукт:
- ШФУ (содержание серы 0,9%) – 79,2% от массы сырья (сера перераспределяется преимущественно в кокс)
- Кокс – 9,3% от массы сырья
- Газы на сжигание (не являются продуктом) – 9,8
- Расход электроэнергии на тонну сырья* – 7,8 кВт*час/тонна сырья
- Обслуживающий персонал – 1 оператор в смену
Фракционный состав по ГОСТ 2177-99 |
оС |
---|---|
Температура начала кипения |
85 |
10% перегоняется при температуре |
150 |
20% перегоняется при температуре |
195 |
30% перегоняется при температуре |
221 |
40% перегоняется при температуре |
268 |
50% перегоняется при температуре |
286 |
60% перегоняется при температуре |
314 |
70% перегоняется при температуре |
335 |
80% перегоняется при температуре |
342 |
90% перегоняется при температуре |
354 |
95% перегоняется при температуре |
360 |
Объемная доля углеводородов по ГОСТ Р 52714-2007 |
% массовые |
---|---|
Олефиновых |
15,7 |
Ароматических |
24,8 |
Бензола |
отсутствие |
- Цетановый индекс: 46,2
- Смазывающая способность по ГОСТ ISO 12156-1 – 212мм
- Кинематическая вязкость при температуре 40оС – 4200 мм*/с
- Зольность – 0.008%
- Коксуемость 10%-ного остатка разгонки (микрометод) – 0.26% масс.
- Кислотное число – 0,37 мгКОН/г
- Температура вспышки в закрытом тигле– 61,5оС