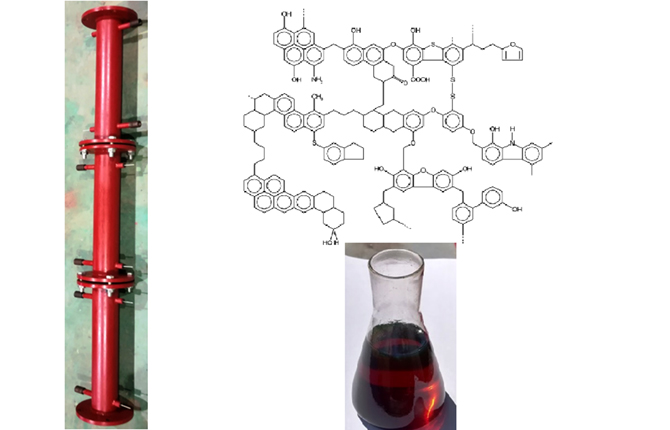
Базовая технология ожижения углей
Гидрогенизация углей – известный процесс, однако большинство методов, экономически нерентабельны (ситуация несколько изменилась с ростом цен на нефть). Это связано с необходимостью применения водородсодержащего газа, высоких давлений (десятки МПа) и температур, катализаторов, с последующей их утилизацией. Предлагаемая технология – лишена этих недостатков. В качестве водородного донора используется вода, в сочетании с неравновесной плазмой. Процесс протекает при околоатмосферном давлении и умеренных температурах. Это позволяет получать синтетическую нефть и нефтепродукты на ее основе, с себестоимостью, даже несколько ниже себестоимости продуктов из природной нефти.
Гидрогенизация углей – известный процесс, однако большинство методов, экономически нерентабельны (ситуация несколько изменилась с ростом цен на нефть). Это связано с необходимостью применения водородсодержащего газа, высоких давлений (десятки МПа) и температур, катализаторов, с последующей их утилизацией. Предлагаемая технология – лишена этих недостатков. В качестве водородного донора используется вода, в сочетании с неравновесной плазмой. Процесс протекает при околоатмосферном давлении и умеренных температурах. Это позволяет получать синтетическую нефть и нефтепродукты из нее с себестоимостью, несколько ниже себестоимости продуктов из природной нефти.
В качестве сырья предпочтительнее использование бурого угля наиболее мелких и недорогих фракций – штыба. Кроме угля, может быть использован каменный уголь низкой степени метаморфизма, а также торф, после стадии частичной термической деструкции, проводимой с целью удаления избытка кислородсодержащих соединений. Степень конверсии горючей части сырья в жидкое топливо – составляет 90-98,5%, в зависимости от типа сырья. Возможна переработка сырья с более высокой зольностью, нежели сырья, перерабатываемого другими способами гидрогенизации.
Технология состоит из последовательно реализуемых стадий, описание которых приводится ниже.
1. Стадия смешения исходного твердого сырья с водой и тяжелым нефтяным остатком
Осуществляется механическим перемешиванием твердого сырья и тяжелого нефтяного остатка (ТНО), в котором диспергирована, с помощью проточного (струйного) кавитационного аппарата, вода.
2. Стадия совмещенного измельчения и предварительной гидрогенизации
Измельчение происходит под действием мощных искровых разрядов, создаваемых специальными разрядными устройствами. После возникновение искры, происходит кавитационное схлопывание искрового канала, приводящее к возникновению ударных волн. Относительно крупные частицы угля, под действием возникающих растягивающих напряжений, дезинтегрируются на более мелки частицы микронного размера. По энергетическим затратам, данный способ сопоставим с механическими способами измельчения, однако имеет существенное преимущества перед ними. Искровой разряд, создает неравновесную плазму, с невысокой температурой ионов (температурой макрообъема) и температурой электронов в несколько тысяч градусов. Наличие электронов с высокой энергией приводит к возникновению радикалов, в т.ч. образуемых при распаде воды и осуществлению реакций предварительной гидрогенизации (ожижения) угля. При этом источником водорода служит не водород содержащий газ, требующий создание дополнительного его производства, а вода. Другим, не менее важным фактором, является то, что значения температуры и давления в искровом канале много больше их критических значений, т.е. вероятен механизм ожижения, характерный ожижению органических твердых биополимеров в сверхкритических жидких средах.
3. Стадия окончательной гидрогенизации
Дисперсную систему, состоящею из частиц твердого сырья, капель воды, ТНО и продуктов частичной гидрогенизации обрабатывают в проточном реакторе неравновесной плазмой барьерного разряда. Плазма барьерного разряда, характеризуется более высоким содержанием активных частиц, нежели искровая, и ее применение, для окончательной гидрогенизации угля, более оправдано с точки зрения энергетических затрат на ведение процесса. Одновременно электроды содержат в качестве диэлектрического барьерного покрытия материал, обладающий каталитическими свойствами. Благодаря последнему, параллельно реакциям гидрогенизации, протекают реакции частичного крекинга, образуемых тяжелых фракций, с увеличением содержания светлых нефтепродуктов, в производимой синтетической нефти.
4. Стадия отделения минерального остатка и выделения ТНО для его рецикла
Отделение минерального остатка осуществляется с помощью центробежных декантеров или иными способами, в зависимости от производительности комплекса по производству искусственной нефти. Выделения ТНО для его рецикла осуществляется ректификацией части синтезированной нефти.
5. Дальнейшая переработка синтетической нефти в товарные нефтепродукты
Может быть осуществлена любыми традиционными методами, поскольку по своему составу синтетическая нефть является подобной нефти естественного происхождения. Также могут быть отдельно предложены альтернативные плазмохимические, кавитационные, каталитические технологии для замены традиционных процессов нефтепереработки.
Преимущества технологии
- Существенное снижение себестоимости синтетической нефти и товарных нефтепродуктов на ее основе. Себестоимость нефтепродуктов – сопоставима или даже несколько ниже себестоимости аналогичных продуктов из добываемой нефти естественного происхождения.
- Простота и надежность оборудования в сочетании с низкими начальными капитальными затратами.
- Невысокие эксплуатационные затраты (ниже в 1,5-3 раза по сравнению с аналогами), поскольку отсутствуют затраты на катализатор и его утилизацию, затраты связанные с получением водородсодержащего газа, а сам процесс проводят в мягких условиях, в отсутствии высоких давлений и температур.
- Высокая степень конверсии (до 98,5%) горючей части исходного сырья в синтетическую нефть. Возможность использований сырья с более высокой зольностью.