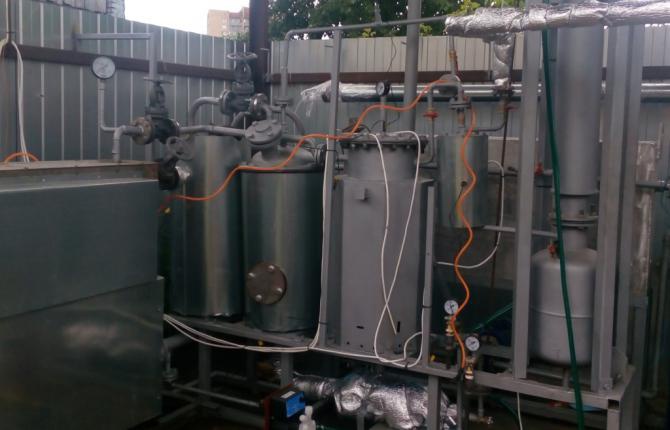
Базовая технология коксование биомассы в среде активированного восстанавливающего газа с целью получения широкой углеводородной фракции
Область использования технологии
Технология предназначена для переработки различных типов сухой (с влажностью менее 20%) биомассы. Под биомассой понимаются такие субстанции.