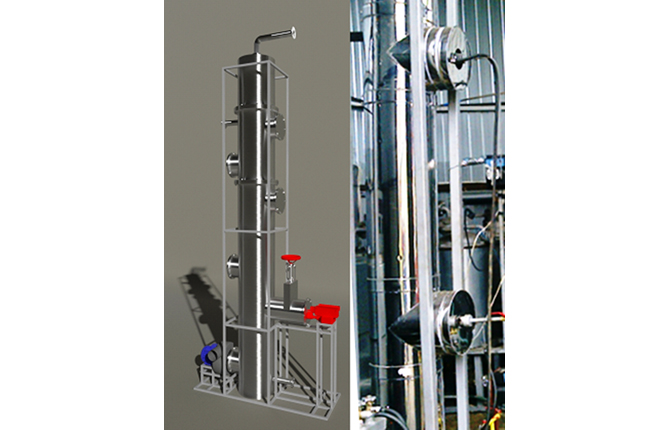
Базовая промышленная технология быстрого пиролиза нефти и нефтепродуктов
Технология относится к нефтехимии и нефтепереработке и предназначена для получения дополнительных количеств бензиновых и дизельных фракций. Перерабатываемым по предлагаемой технологии быстрого пиролиза сырьем могут являться нефтешламы, мазут, сырая нефть. Перерабатываемые нефтепродукты могут иметь высокую степень обводненности (до 50-55%), загрязнения механическими примесями (песком) и содержать высокий процент минеральных солей. Реализуемый, согласно рассматриваемой технологии, процесс не требует внешних энергетических затрат, а оборудование для его реализации работает при околоатмосферном давлении и отличается простотой и надежностью. Дополнительными возможностями технологии являются частичное обессеривание и деметаллизация нефтепродуктов, выработка электроэнергии, исключение процессов обессоливания и обезвоживания сырой нефти.
Типичный баланс процесса быстрого пиролиза
Состав сырья пиролиза (сырой нефти) |
Состав продукта пиролиза |
Фракции с температурой кипения
Примечание. Содержание серы 0,5% . |
Топливные фракции с температурой кипения 80-300оС (в расчете на исходную сухую нефть) 69,3%
Примечание. Содержание серы 0,1%. |
Неорганические компоненты (песок) – 0,50% |
Неконденсирующиеся газы (С1…С4) – 4,7% |
Вода – 8,2% |
Водный конденсат – 8,2% |
Фракции с температурой кипения более |
Коксовый продукт и зольный остаток – остальное.
Примечание. Коксовый продукт используется в качестве энергоносителя (выжигается кислородом воздуха). Образующийся коксовый продукт избыточен по отношению к энергетической потребности процесса быстрого пиролиза. Его избыток может быть использован для выработки синтез газа, водородсодержащего газа или получения технологического пара. |
Технология реализуется на специальном реакторе быстрого пиролиза с твердой насадкой, а процесс пиролиза реализуется при околоатмосферном давлении без использования внешних энергоресурсов. Реактор быстрого пиролиза выполнен в виде отдельного аппарата, внутри которого содержится определенным образом размещенная твердая насадка. Насадка изготавливается из огнеупорного материала с определенными значениями теплоемкости и теплопроводности. Реактор также содержит специальные горелки для его первоначального запуска, систему воздушного дутья и систему отвода парогазовых продуктов пиролиза. Процесс пиролиза реализуется следующим образом. В вертикально расположенном цилиндрическом реакторе осуществляют первоначальный нагрев насадки таким образом, что создают вертикальный градиент температуры со значением температуры верхнего слоя насадки 573-673К и значением температуры нижнего слоя насадки 873-1073К. При первоначальном «холодном» пуске реактора упомянутый нагрев осуществляется с помощью специальных горелок, размещенных в реакторе. После разогрева насадки сверху в реактор подают сырье – жидкие нефтепродукты (мазут, в том числе обводненный), нефтешламы, сырую или подготовленную нефть. Контакт нефтепродуктов с нагретой насадкой позволяет реализовать процессы грубого разделения сырья на фракции, крекинга и коксования сырья. Совмещение упомянутых процессов в одном реакторе и в одном цикле возможны из-за наличия в реакторе вертикального градиента температуры насадки. Вначале по мере продвижения нефтепродукта вниз по насадке из реактора выходят пары воды, если она содержалась в сырье, и углеводородные фракции с температурой кипения меньшей, чем 623К. Таким образом, термическому крекингу подвергаются в основном только фракции, имеющие температуру кипения большую заданного значения. При этом образующиеся в процессе крекинга топливные фракции также быстро выделяют в газообразном виде из насадки и не подвергают длительному крекингу, в котором из них могли бы образоваться неконденсирующиеся газ и кокс, за счет чего увеличивается выход топливных фракций. Фракции, с большей температурой кипения, опускаются вниз по горячей насадке и подвергаются крекингу и коксованию. За счет специальной геометрии насадки при интенсивном вскипании пленки нефтепродукта, процесс крекинга сопровождается кавитационными явлениями, обусловленных схлопыванием образующихся паровых пузырьков. Последним, видимо, может быть объяснен пониженный выход газообразных продуктов крекинга, благодаря перераспределению атомов водорода в продуктах процесса быстрого пиролиза. Продукты крекинга и разделения сырья на фракции выходят из реактора в виде паров, охлаждают, либо подают в виде пара на ректификационную колонну для более тщательного их разделения. Фракции с температурой кипения 353-623К используют для производства моторного топлива, неконденсирующиеся горючие газы служат источником тепла для сторонних потребителей или генерации электроэнергии.
После охлаждения насадки в процессах разделения сырья на фракции и крекинга прекращают подачу сырья в реактор сверху, снова нагревают насадку и создают в ней вышеупомянутый градиент температуры. Для этого снизу в реактор подают воздух, поджигают пламя внизу реактора и выжигают кокс, образовавшийся на насадке в процессах крекинга и коксования сырья. Продукты сгорания кокса и горючих газов, частично охлажденные при нагреве насадки, выводят из ректора сверху и используют для нагрева сырья перед его подачей в реактор. Тепло, образуемое при сгорании кокса, избыточно по отношению к теплу необходимому для нагрева насадки и может быть реализовано сторонним потребителям (например, в качестве технологического тепла, необходимого для ведения других технологических процессов), либо использовано для генерации электроэнергии. Также в зависимости от варианта исполнения реактора при выжигании кокса возможна подача водяного пара с целью получения синтез-газа или водородсодержащего газа.
По завершению процесса выжигания коксового остатка и автоматического удаления зольного остатка, повторяют технологический цикл, включающий процессы разделения сырья на фракции, крекинга и коксования.
Пример возможной реализации колонны быстрого пиролиза и стендовая установка
Преимущества и возможности технологии
- Возможность переработки сырой неподготовленной нефти с высоким процентом содержания воды. При внедрении технологии снимается необходимость дорогостоящих операций обезвоживания и обессоливания нефти. Снижаются расходы на транспортировку высоковязких нефтей. Другим преимуществом переработки сырой нефти является то, что снимается проблема с накоплением подтоварной воды, поскольку водный конденсат не содержит солей и может использоваться как техническая вода, либо безопасно сброшен в водоемы.
- Возможность включения в состав верхних секций колонны быстрого пиролиза каталитической секции изомеризации, позволяющих получать зимние топлива и высокооктановые бензины за один цикл переработки сырья.
- Возможность переработки нефтешламов и обводненных мазутов. Нет необходимости в предварительном разделении нефтешламов на углеводородную составляющею, механические минеральные примеси и воду.
- Возможность переработки нефтепродуктов с выработкой тепла и электроэнергии. Например, при комплексной переработке мазута, включая сильнообводненного, получаемая дизельная фракция выше стоимости мазута необходимого для ее производства, а генерируемое тепло – может использоваться для выработки электроэнергии и отопления. Также тепло (греющий пар) и электроэнергия могут быть востребованны непосредственно в месте нефтедобычи.
- Возможность выработки синтез-газа или водородсодержащего газа.
- Частичное обессеривание и деметаллизация получаемых продуктов. В ходе процесса происходит перераспределение серы и металлов, содержащихся в исходных нефтепродуктах. Большая часть серы и практически все металлы остаются в коксе, в то время как отгоняемые из реактора светлые фракции содержат их существенно меньше. Зола, образуемая при выжигании кокса, может служить источником для получения цветных металлов.
- Низкие капитальные и эксплуатационные затраты за счет простоты конструкции оборудования.
- Надежность оборудования и отсутствие высоких и остаточных давлений в процессе, что повышает его безопасность и упрощает эксплуатацию.